F.A.Q’s
Frequently Asked Questions
Our ‘RenoFlor’ solution is a modern, innovative and cost-effective existing concrete floor polishing system.
The solution restores concrete floors back to their pre-let build condition through a micro-grind, densification and sealing process.
The ‘RenoFlor’ solution is more environmentally friendly than traditional methods, reduced future maintenance liabilities and provides a 10 year guarantee.
The design of any concrete floor slab can only take place properly if all the other necessary information has been concluded in terms of what is underneath the floor, what is going on top of the floor and how is it to be constructed and for what use. In designing concrete floor slabs we also have to consider other aspects, such as cost plans, programme implications, design lifespan, ongoing maintenance and recycling suitability in the long term. We can add various different admixtures to the concrete and or concrete surface which will enhance the aesthetics of your concrete floor and provide you with a beautiful polished concrete finish.
Another important question when selecting options for constructing and designing a concrete floor slab is what the most common use of the floor will actually entail. From food factories to waste recycling facilities and high bay racking with narrow aisle warehouses we have experience in both constructing and maintaining the concrete floor slabs. A full appreciation of what the tenant and end users require needs to be ascertained in order to provide the best solution to suit the needs and requirements. It is therefore vitally important the specification of the floor is discussed at design stages to enable Level Best Concrete Flooring to be able to provide the best long term solution.
The question often arises as to how one should choose or select a suitable concrete flooring maintenance contractor from a list of tendering contractors. Simply looking at pretty pictures on websites or pushy sales people offering extremely competitive prices is not often the best solution. Whether the contractor is the oldest or the largest or the cheapest or the busiest flooring contractor does not mean they are the best choice for your project. References are advisable but do not always guarantee success if the project you are requiring is totally different to from the job detail in the references. The references should ideally be relevant and as recent as possible. Site visits during works on other projects can be beneficial to clients to allow them the opportunity to view the various processes, competency of staff and appearance of the finished product. It is common for other ideas to derive from site visits as well, which also help to improve the successfulness of the proposed flooring project. Albeit image is not everything, it can be important when considering the right contractor, especially in terms of plant and equipment. Everything relating to concrete is expensive from the equipment itself right through to the product. Ensure that the flooring contractor has the correct resources in place along with flexibility in case things go wrong. At Level Best Concrete Flooring we can provide you with an extensive number of references and testimonials, which help confirm you have made the right choice in choosing us.
The products we apply to the concrete floor are clear and hence do not have a colour. It is impossible to achieve colour uniformity, as concrete is produced using natural materials that vary immensely in colour. Our floor coating systems we apply assist us in providing clients with a long lasting and aesthetically pleasing and durable surface which is extremely difficult to remove without deep grinding.
Concrete is an absolutely marvellous product with many benefits and useful features. The only unfortunate problem with the product is the tendency to crack, especially in the early life of the floor slab and sometimes not were expected. Providing clients are aware of this as well as other potential issues then complaints are less likely. An understanding of shrinkage and movement can also prove beneficial so that full knowledge of what the floor will look like and perform is learned. An agreed list of snagging items on completion of the floor slab and the best time to conduct these snags should be sensibly agreed between all parties. Concrete is laid wet, and like anything that contains water, it shrinks. This shrinkage can take place over many years with the bulk of the shrinkage taking place during the first 6 months. With this in mind it is sometimes better to carry out snagging items such as sealing perimeter joints or repairing small cracks, following a period of approximately 12 months, to allow for the movement of the floor slab from caused by shrinkage.
If you have an ageing floor slab with lots of cracks, racking bolt fixings, damaged joints and other repairs, then Level Best Concrete Flooring can provide you with free survey costs, which will also detail timescales in which we can carry out the works for you.
Building occupiers must understand that housekeeping and general maintenance of their concrete floor is of paramount importance to minimise expensive repair costs. Regular floor cleaning, rather than driving grime and debris into the floor slab, helps far more than most end users realise. Floor joints should be inspected and monitored by a reputable contractor with surveys kept on record in order to manage the costs and spend money wisely on an annual basis. Once the maintenance management system is put into practice and expenditure controlled consistently, long term costs and downtime to the logistic operations is drastically reduced. In comparison if a car is regularly serviced and maintained, the chances of breakdowns reduce and a concrete floor is no different. Cracks are more difficult to monitor and hence the need for an experienced concrete flooring contractor. Albeit cracks may be visible, repair might not be required if the floor remains serviceable and movement stable. Once a full understanding of the floor has been appraised, sensible solutions should be proposed and agreed.
Level Best Concrete Flooring are the flooring contractor of choice to many clients for their annual planned maintenance budgets. We work on bank holidays and shutdown periods for many blue chip clients such as Fedex, Prologis, Vauxhall, Encon and Screwfix.
Concrete floor joints and the various types available can cost building owners and occupiers a lot of money if either positioned incorrectly or the wrong type used. Joints in narrow aisle warehouses for example take a constant pounding on a daily basis in exactly the same location. When discussing joint types with your flooring contractor ensure that you are getting the best solution enabling as smooth a transition as possible. If the floor has been laid correctly with the right reinforcement, the only place it can really start to fail or cost money is at the joints. It should also be noted that using high dosages of steel fibre reinforcement or heavy steel bar, jointless floor slab designs are possible. The term jointless means there are no saw cut induced contraction joints required. This sounds fantastic in principle but clients should be aware that the slabs shrink far more at the main construction joints and also perimeter. This can cause quite large cracks to appear if the floor is loaded quite early or raking installed which pins the slab and restrains shrinkage. If floor loading can be left for a few months the jointless floors crack far less and are a great solution. More commonly seen in the UK, especially with ground bearing floor slabs are steel fabric designed floors with traditional saw cut joints. Joints should be positioned underneath racking and not within aisles to minimize trafficking and avoid breakdown. The saw cut joints should be sealed to help protect the edges of the joint and minimise spalling. There are innovative joint sealants on the market such as Instant Seal 101 and 102. The Instant Seal 101 immediately seals the saw cut joint once the joint has been installed within the floor. Instant Seal 102 is a wider sealant strip for saw cut joints which have been carried out previously but now require sealing either for the first time or following increased movement. In the past construction joints also known as day joints were and still are constructed using timber or steel road forms with dowel bars installed at anything from 300mm to 600mm centres. Technical advancements over the years has seen the introduction of steel profile permanent floor joints. These joints provide armoured protection to the arris edge of the floor joint along with full load transfer under trafficking. The joints have proven to be cost effective in the long term for the building owners. Joints can also be manufactured in stainless steel which is ideal especially in food factories or for hygiene reasons or instances when the floor becomes wet near doorways or from washing down areas. The location of these joints becomes more critical though due to the fact they are a permanent feature of the floor. If the joint is positioned incorrectly such as in an aisle or main traffic route it will eventually start to breakdown and repairs can be extremely expensive. A plan showing joint locations and positions for all relevant parties to comment on and review, should be provided to eliminate any problems once the floor has been cast.
Level Best Concrete Flooring can provide you with many different floor joint repair systems to improve the longevity of your concrete floor slab. Our floor surveyors will visit your premises and provide a full breakdown of cost and timescales to provide you with an excellently performing concrete floor.
Warehouse and factory concrete floor slabs are used by many different manufactures and distributors throughout the United Kingdom. Careful planning must take place prior to the agreement of the required flatness tolerances within the new building. If the warehouse is to receive high bay racking with wire guided fork lifts then a defined movement tolerance should be selected as the fork lift only travels on the same wheel path. If a floor has wide aisle racking without wire guided trucks, then a free movement tolerance is more suitable. Food factories usually have drainage installed within the concrete floor and hence falls within the floor are required to allow liquids to fall into the drains and gulleys. External hardstandings are also usually laid to falls to minimize standing water following heavy rain. The basic principles need to be considered that if the falls are only slight the water will not usually fall on its own and other methods will need to be considered in order to help move standing water. If the falls are too great, then it may cause difficulties when loading wagons or trailors on steep inclines. These conversations should be discussed and agreed with the end user and flooring contractor prior to any concrete being laid, as once the floor is complete it is almost impossible to rectify successfully.
If you can tell us your problems with the flatness of your concrete floor, we can almost always provide you with a solution. We also remove and replace existing concrete floors as part of our service range provided to clients. If the concrete floor is beyond repair then sometimes the only other solution is to remove and replace with a high strength structural concrete floor replacement. Our team has the knowledge on how to design the repairs to suit the usage of the buildings
Yes we have a full nationwide coverage, including the Channel Islands. We recently carried out some anti slip flooring at a waste recycling centre in Guernsey as one example.
WHY YOU SHOULD CONSIDER F.R.S
- Increased Aesthetics
- Improved Structural Integrity
- Cost Effective
- Resistant to Scratching & Staining
- 100% Dust Free
- Durable & Abrasion Resistant
What our customers say
“I managed a warehouse which was in a very poor condition. The main issue we had with the floor was the constant collection of dust on the floor surface, disrupting the day-to-day storage and despatch of goods. The warehouse floor was also extremely difficult to clean and heavily stained. The numerous layers of floor paint we had applied over the years were building up and line marking was becoming difficult to distinguish and becoming no use.
Going forward we wanted a warehouse floor which was dustproof, easy to clean and easy to manage. On top of a floor which would perform better in service, we wanted it to be aesthetically pleasing for when the client visits the warehouse. We felt the best way to increase the aesthetics of our warehouse floor was to make it a light-reflective and brighter surface.
That’s where Level Best Concrete Flooring’s Floor Renovation System came in. They approached me with this very quick system and process which transferred our old warehouse floor. The polishing system ticked all the boxes we wanted ticking – leaving the floor dust-proof, easy to clean, easy to line mark, more aesthetically pleasing and light-reflective. The finished product looked amazing and improved the overall functionality of the warehouse.”
Douglas McTaggart, Warehouse Manager
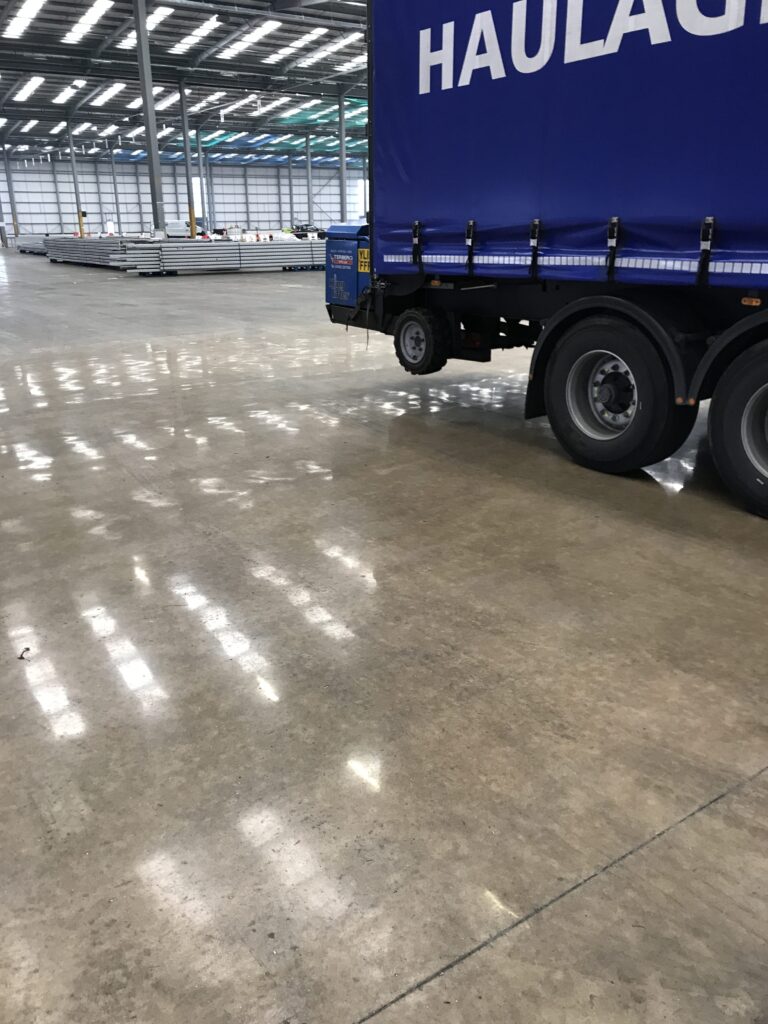
SUITABLE APPLICATION AREAS...
- Factories
- Industrial Units
- Distribution Warehouses
- Storage Warehouses
- Showrooms
- Retail Stores